A Yainville, l’aventure débute en 1930. Mais le savon c’est vieux comme le monde. Marchandise rare, donc chère, il faudra attendre le milieu du siècle pour trouver le savon de Marseille. Le produit restait coûteux, c’est pourquoi nos arrière-grand-mères ne l’utilisaient pas pour laver leur linge. Alors comment procédaient-elles ? Elles tamisaient des cendres de bois, de préférence de hêtre, les lavaient, les mélangeaient avec de la chaux vive et y ajoutaient des orties séchées. Il fallait 2 kg de cendres pour 100 kg de linge. Cela semble beaucoup mais autrefois on lavait une ou deux fois par an. Nos aïeules faisaient bouillir le linge, mais jamais le vendredi et surtout pas au mois de mai. Allez savoir pourquoi ! Cette façon de procéder dure jusqu’à la Grande Guerre, époque où le savon de Marseille devint un produit de consommation courante. Chez l’épicier du village, une seule marque de savon est à vendre. Les ménagères le stockaient pour qu’il sèche. Il arrivait en caisses, les fameuses caisses à savon.
Les premières savonneries s’installent à Marseille car les matières premières, l’arachide, le coprah-palmiste débarquent dans le port. La demande est telle que les savonniers marseillais décident de construire une usine dans “le nord” pour se rapprocher des marchés parisiens. Yainville est choisi pour son site : Au bord de la Seine, on peut débarquer les matières premières dans l’usine. La route, la ligne de chemin de fer sont des atouts. Le projet prend forme en 1930. Le principal investisseur est la société Fournier-Ferrier, un savonnier marseillais. Par l’intermédiaire de ses filiales, la Compagnie des Produits Électrolytiques à laquelle elle prête les fonds nécessaires, la Société Havraise d’énergie électrique participe aux dépenses de constructions pour un quart. Les reste se partage entre la Société des coopératives de France, le groupe Worms, l’Office public des habitations bon marché. La future savonnerie prend le nom de Société normande des corps gras.
Roland Edde passait chaque jour devant le chantier pour se rendre à l’école :
«Nous étions étonnés par la taille des tracteurs à chenilles qui taillaient dans la falaise».
Justement on pourrait penser que le site est mal choisi car le haut de la falaise surplombe la Seine du 30 mètres :
«mais elle a été rognée, consolidée, soutenue, rectifiée et semble maintenant n’exister que pour permettre une fabrication en paliers. Les étapes successives du travail se faisant pas descentes naturelles d’opération en opération».
Des photos d’époque nous permettent de dater les phases finales des travaux. En avril 1933, l’ossature de l’ensemble des constructions est en place. Les plus importantes se situent au niveau de la D982 : côté centrale électrique le bâtiment de traitement des corps gras; à toucher “la cathédrale”. Les anciens baptisaient ainsi la grande bâtisse aujourd’hui détruite. C’était un véritable blockhaus pour sa solidité. Imaginons la couper en deux. Côté Seine on trouve des ateliers de fabrications. Du côté de la route, deux niveaux de bureaux, puis, au-dessus, des cuves qui contiennent au total 1200 tonnes de matières premières, puis encore au-dessus, un réservoir d’eau de 250 mètres cubes. Une belle charge sur la tête des employés.
«Les plafonds étaient un peu humides… mais loin de nous la pensée que cela pouvait nous tomber dessus».
Au faîte du toit, en 1964, on inscrira : “Savon Le Chat”. Ce bâtiment de grande taille avec sa toiture en queue de geai et ses colombages se voulait de style néo-normand. Avait-on choisi de construire dans le caractère des nouvelles maisons du Trait ? En descendant d’un palier, on arrive au niveau de l’atelier de fabrication du savon. Au plan inférieur : celui du conditionnement est suivi des magasins d’expédition, situé le long de la Seine. La petite tour carrée surmontée d’une girouette n’est pas là pour le décor. Elle renferme le monte-charge qui permet d’élever les fûts de matières premières au niveau du stockage. Mais on se souvient des 135 marches à descendre ou à monter entre le haut et le bas de l’usine. Entre la centrale et la savonnerie, un tunnel est foré pour y passer un tuyau. La centrale fournira à l’usine de la vapeur aux heures creuses. Nous sommes avant 1939, au cours des années les diverses fabrications exigeront de nouvelles constructions.
Une enquête de commodo et incommodo menée en septembre 1932 relative à l’installation de la savonnerie trouves des personnes hostiles. Le propriétaire de l’abbaye de Jumièges s’y oppose formellement. Celui du manoir de Yainville “chez les Zoaques” craint des odeurs nauséabondes et des vapeurs. Le président des œuvres sociales du Trait appréhende pour la santé. Un autre trouve que la savonnerie dépare le paysage bien plus que la goudronnerie. La production démarre fin 1934, on ne fabrique que du savon de Marseille. Le 21 mars 1935, le maire d’Heurteauville, à cause des odeurs, dépose une plainte. Par la suite les choses rentrent dans l’ordre. A savoir si les odeurs diminuent ou ben que les gens s’habituent.
Si les premiers cadres viennent de Marseille, la main-d’œuvre est locale. On n’embauche pas d’ouvriers qualifiés sauf pour les services d’entretien. Les futurs agents de maîtrise, voire même les ingénieurs-maison seront des hommes formés dans l’usine. La moitié du personnel est féminin. Ces femmes habitent souvent le Trait. Est-ce la raison pour laquelle le groupe Worms a investi dans la nouvelle savonnerie ? En procurant du travail aux épouses, il fixait les maris au chantier naval. A cette époque pour quelques francs de plus on changeait de patron.
Les témoins d’avant-guerre sont rares. Les hommes fabriquent le savon. Pas de femme autour des chaudrons… Les méthodes changeront peu, sauf qu’à cette époque on le coule dans des plaques refroidies à l’eau. L’usine de Yainville est une des premières à utiliser ce nouveau procédé. Avant on étalait le savon sur un sol cimenté. Les femmes travaillaient au conditionnement. Elles se souviennent, les images refont surface :
«Sorti des cadres, le savon était découpé en cubes par des fils d’acier. Puis nous les rangions sur des clayettes pour les passer au séchoir: Sec, chaque morceau placé dans une forme était frappé, on lui imprégnait la marque du savon. Avec la main gauche, on mettait le morceau dans le moule, avec la droite on le retirait. Cette machine était dangereuse, plus d’une y a laissé un bout de doigt. Après, le savon était mis en caisse ou en carton. Au bout de la chaîne c’était un homme qui les prenait. Tout ça c’était avant la guerre, et ça durera plusieurs années après».
Vers 1938, la savonnerie débute la transformation de la glycérine qui arrivait brute. Il fallait la distiller. Ces travaux s’effectuaient de nuit, aux heures creuses de la centrale qui fournissait la vapeur :
«C’était payé 15 heures pour 12 de présence, du tout bon, car en quatre jours nous faisions nos 60 heures».
Les grèves de 1936, le Front populaire, rapprochent un peu plus les salariés :
«Nous partions en cortège pour défiler au Trait. Les salaires qui augmentaient, les congés payés, quelle belle époque ! Malheureusement une bien courte embellie. Oui, nous étions mieux payées que les filles qui travaillaient dans les filatures. Ce n’est pas pour ça que nos patrons étaient des tendres. Je me souviens d’un jeune ingénieur de chez nous. Après le Front populaire, ils ont trouvé une raison pour le virer : une erreur d’excès de soude. Mais le réel motif est qu’il manifestait avec nous».
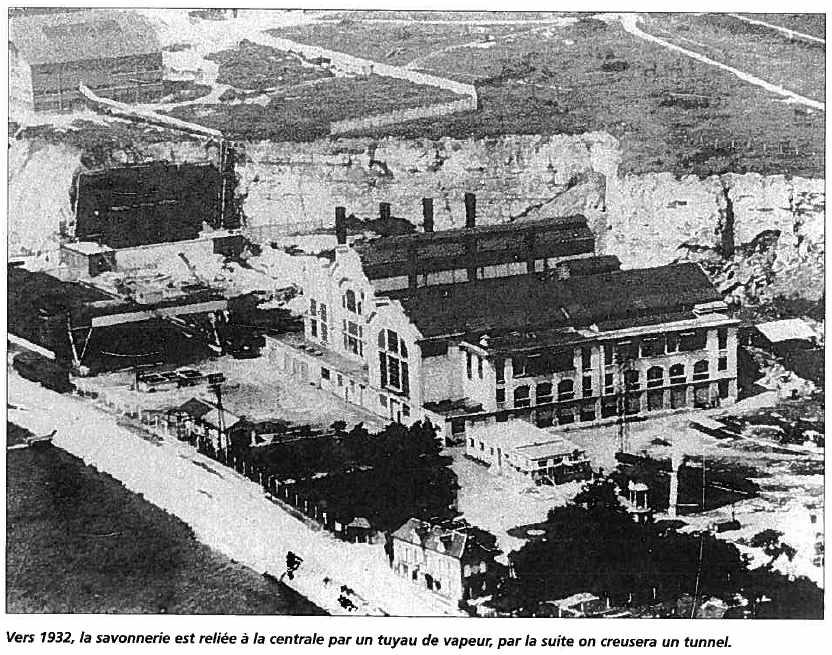
La savonnerie tourne bien, la guerre va ralentir ce bon départ. En septembre 1939, les hommes mobilisables partent, on embauche des femmes, des retraités reviennent. Faute de courant électrique l’usine s‘arrête. Le 9 juin 1940, tous partent en exode. Les fumées des raffineries sabotées obscurcissent le ciel bleu. Aucun ordre de destruction de la savonnerie n’a été donné. Deux jours plus tard les Allemands arrivent. Après la réunion des chefs d’entreprises industrielles à Rouen le 26 juin, l’occupant ordonne la remise en marche des usines. Naturellement il faut fournir des produits aux Allemands. Les matières premières font défaut. Les relations maritimes avec nos colonies deviennent difficiles et nulles à partir de fin 1942. Plus d’arachide, plus de coprah, il reste les graisses animales et bientôt les oléagineux locaux. Dans nos régions on cultive le colza et le soja, au sud le tournesol. Pour diversifier ses fabrications, la direction décide en 1943, de construire des unités de broyage et d’extraction des graines d’oléagineux, c‘est toute la partie de l’usine qui deviendra l’huilerie. En avril 1944, le premier jet d’huile de colza est obtenu. Mais laissons un ancien nous parler de cette époque :
«Nous fabriquions du savon chargé de kaolin qui contenait 11 à 15% de matières grasses. Nous mettions dedans tous les corps gras que l’on trouvait. Si on jetait un morceau de savon dans l’eau, cinq heures après il restait du sable dans le fond du seau. Pour les Allemands il était plus gras. En 1941, on produisait de la lessive en poudre à base de soude, de bicarbonate, d’acides gras et d’eau. Nous faisions tout sur place, y compris les caisses à savon en bois. Plus de 200 femmes travaillaient dans l’usine. En 1942, des hommes partent en Allemagne, une vingtaine de S.T.O. Les Allemands venaient pour contrôler; mais ne restaient pas sur place. A l’époque c’était dur de trouver du ravitaillement. Les gens de la savonnerie troquaient du savon contre des vivres chez les cultivateurs de la région. Nous allions voir les cousins paysans perdus de vue».
Sur le sujet on nous raconte une anecdote :
«Le Directeur avant l’arrivée des Allemands, avait caché plusieurs palettes de morceaux de savon. La cachette était bonne. A la Libération il va pouvoir les récupérer. Extérieurement elles avaient gardé le même aspect, des blocs d’un mètre cube. La surprise : à l’intérieur il n’y avait plus rien, le milieu avait été creusé par des gens qui peut-être avaient des cousins cultivateurs !».
Malgré les événements, les hommes ne désespèrent pas. Pour preuve, ils ont construit l’huilerie et trois maisons dans le haut de la côte Béchére pour y loger des cadres de l’usine. C’était prendre des risques, car la guerre ne va pas épargner le site. Centrale électrique, savonnerie, pour un bombardier en altitude ça ne faisait qu’un. Et quand les bombes tombent dans le cimetière de l’église du Trait, le 4 août 1943, qui était visé ? Les usines de Yainville ou le chantier naval ? L’entreprise Bai, construit un abri antiaérien sous la falaise. Aux alertes les employés qui travaillent en haut préfèrent fuir vers la forêt pour s’écarter de l’usine, c’était plus rapide que de descendre les 135 marches. Le premier bombardement a lieu le 6 juillet 1941. Puis le 19 avril 1943, suivi d’attaques les 29 et 30 juillet. La presse annonce que la savonnerie est en partie détruite. Après, un poste de surveillance est installé sur la rive gauche. Au bruit des avions le guetteur ou la guetteuse sifflait, l’alerte était donnée dans l’usine. Les Allemands avaient mis en place une pièce de DCA de quatre tubes de 20 mm au lieu-dit le Boel, situé entre la savonnerie et le vieux Trait. Est-ce cette pièce qui abat le 21 mai 1944 un Spitfire anglais qui tombe dans la plaine de Yainville ?
Les Allemands ne retrouveront pas le pilote, la Résistance, oui. La DCA, entre le Trait et Yainville ne manquait pas : plus d’une vingtaine de batteries. Le pire restait à venir pendant les derniers jours de |’occupation car le bac de Yainville devient la cible des avions Alliés, en plus les obus tombent sur les usines les 28, 29 et 30 août. Les derniers Allemands avant de partir mettent le feu à l’atelier de la caisserie. La guerre n‘aura pas épargné les vies humaines. M. Auger sera tué au cours d’un bombardement. Maurice Lefebvre déporté politique et M. Foucault, STO décéderont en Allemagne.
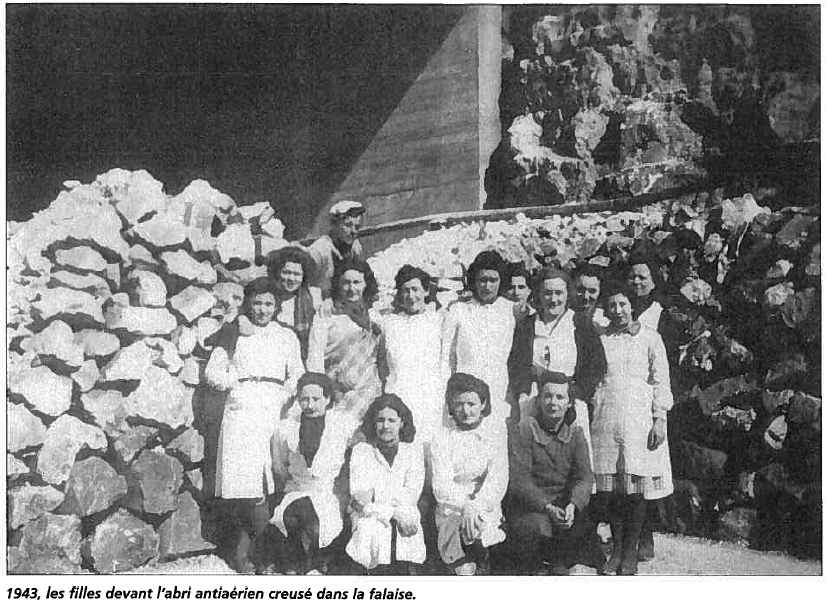
Les Allemands avant de quitter Yainville, n’hésitent pas à saboter la centrale électrique. Pas très correct, en 1940 nous l’avions laissée en état… Toutes les usines locales sont tributaires de la distribution de l‘énergie. En attendant, tous remettent les lieux en état de bon fonctionnement. Comme par hasard, on retrouve des matières premières destinées aux Allemands. On redémarre la fabrication du savon. Les premiers navires vont accoster de nouveau. En 1945, commence l’extraction d’huile d‘arachide à Yainville. Une anecdote sur le sujet bien dans le contexte de cette époque :
«Un jeune ingénieur qui habitait Rouen, chaque jour venait travailler à l’usine en vélo. Le midi, il reprenait sa bicyclette pour aller déjeuner à Duclair. Le jour du premier jet d’huile d’arachide, le restaurateur est tout fier de lui servir des frites faites avec de l’huile d’arachide… et elle vient de Yainville monsieur !».
Le circuit du marché était si court, que le produit arrivait avant sa mise en vente.
Le 1er septembre 1947, la savonnerie se sépare des ateliers de fabrication de l’huile qui deviennent une entreprise indépendante : la Société normande d‘huilerie. A Yainville on dit : « Les Coop reprennent leurs billes».
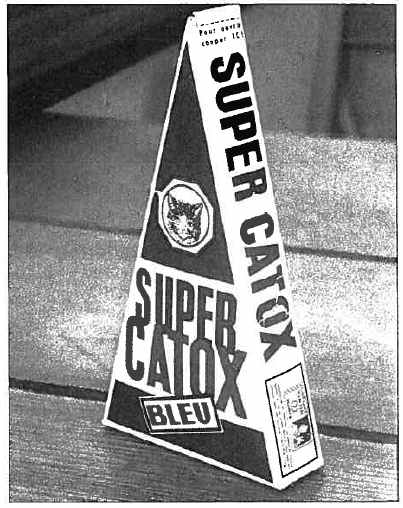
Les chercheurs des établissements Fournier-Ferrier inventent un nouveau produit de poudre à laver. Dans les immeubles, il n’y a plus de buanderie, les lessiveuses à ébullition aspergeaient automatiquement le linge mais les lessives moussaient de trop. On risquait d’inonder l’appartement. C’est ainsi qu’est née la poudre à laver qui ne mousse pas. A cette époque on ne connait pas encore les tissus synthétiques, on faisait bouillir le linge. On demande à l’usine de Yainville de fabriquer le Catox. On décide en 1949 de monter des bâtiments neufs. La poudre se fait dans des appareils où l’addition de tous les produits nécessaires (mouillants, moussants et détergents) donne des blocs qui sont concassés, broyés, pulvérisés pour finalement être conditionnés. Cette fabrication devant la demande toujours accrue de la clientèle, va prendre beaucoup d’importance. Un exemple, le 12 octobre 1950, l’usine produit 26,292 tonnes de Catox, dans le mois 665,93 tonnes. La main-d’œuvre est surtout féminine : 84 femmes et 18 hommes. Le travail s’effectue en deux quarts journaliers, de huit heures. Du Catox on en parle encore dans les chaumières ! Ce sera une des premières campagnes de publicité digne de ce nom :
«Employez tous Catox et sans vous fatiguer votre linge sera bien lavé».
C’était le slogan de l’émission de radio (la télé n’existait pas) « Reine d’un jour ». Jean Nohain et le géant Atlas, viennent visiter l’usine et tout le monde est invité à l’émission au cirque de Rouen, quelle journée ! Pour fabriquer le Catox les conditions de travail sont pénibles. Des dames se souviennent et parlent entre-elles :
«Ca rongeait le bout des doigts, ça collait l’hiver, de la poussière l’été. Nous touchions des blouses et un petit chapeau, mais à la fin du quart nous étions toutes rouquines. Tu te souviens ? Avant qu’ils mettent du carrelage, nous mettions des sabots. Les emballages arrivaient à plat. Nous les montions, un coup de pinceau pour mettre la colle. Le Catox descendait de l’étage par un entonnoir. Un maillet pour taper sur la goulotte car le Catox se bloquait. Nous touchions une prime et du lait… Nous étions cinq par table pour remplir les paquets. Un coup de colle pour les fermer. Si il n’y avait pas de stock de produit, pour prendre de l’avance on montait des boîtes. Après on a déménagé, c’était mieux, il y avait un dépoussiérage d’air».
A Marseille se monte une tour de 50 mètres pour améliorer la production du Catox. Il est décidé d’en construire une à Yainville. Les travaux sont abandonnés, car le concurrent Omo prend le marché. En 1955, on ne fabrique plus de Catox à Yainville.
Bientôt les savonniers doivent s’adapter aux textiles artificiels et aux machines à laver. Et, chacun se lance dans des recherches techniques pour devancer ou suivre la concurrence.
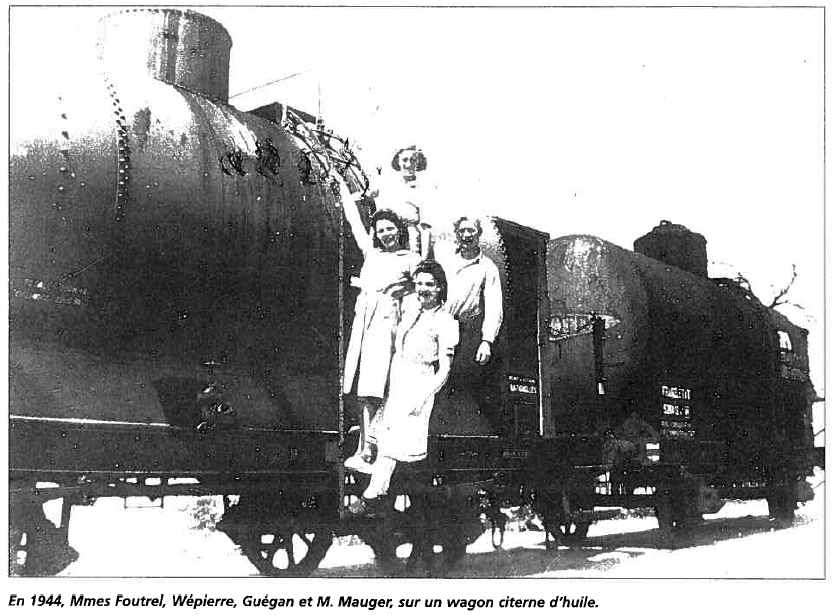
Dorénavant le produit essentiel ici sera le savon. Les besoins en vapeur augmentent. En 1952, il est décidé de mettre en place une chaudière de 32 bars, puis en 1953 une deuxième de 32 bars. L’atelier de glycérine devient autonome grâce à deux petites chaudières. La savonnerie n’est plus tributaire de la vapeur fournie par la centrale électrique. Et l’eau ? Elle était prélevée dans quatre puits. La savonnerie employait énormément d’eau : trois millions de mètres cubes en 1963. Une station d’épuration des eaux résiduaires sera construite.
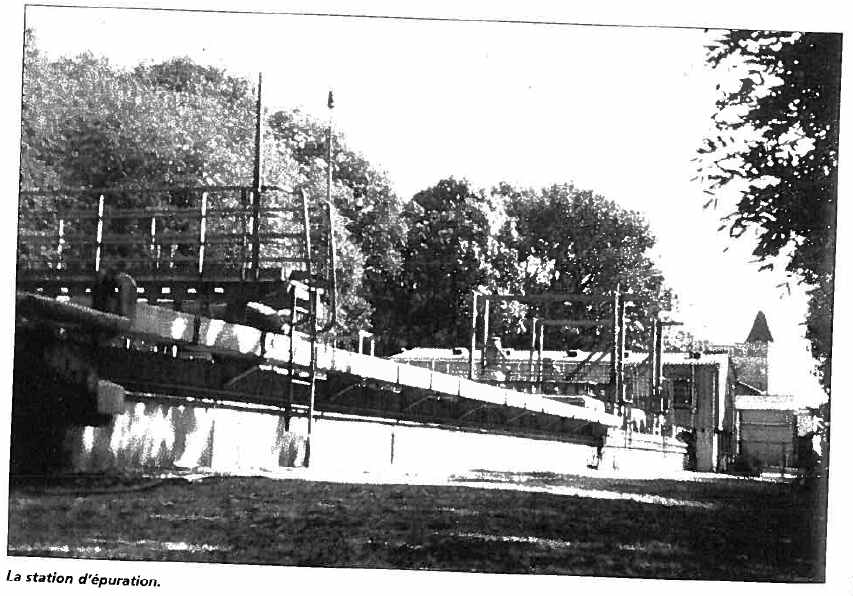
La fin de Catox n’amène pas de licenciement. Toujours ce souci de créer, de fabriquer un nouveau produit. En 1954, Yainville est le premier au monde à fabriquer le savon translucide sous le nom de Chat ambré. Mais pourquoi le chat ?
«Par tradition, les savonniers donnaient des noms d’animaux ou de plantes à leurs savons».
En 1959, la Société normande des corps gras va changer d’appellation. Elle entre dans le groupe Unipol et devient “Nouvelles savonneries françaises”. On arrive dorénavant dans l’ère de la grande consommation, les clientes dans les supermarchés se servent elles-mêmes. L’emballage devient important. L’image vue à la télé, dans la presse guide le choix. En 1962 Unipol investit 7,5% de son budget en publicité et frais commerciaux.
La savonnerie emploie 310 personnes, fabrique 15.000 tonnes de savon, 5.000 tonnes de glycérine et 5.000 tonnes de produits industriels.
A partir de cette date, les techniques de fabrication évoluent, mais les ingrédients restent les mêmes. Dans la cour de l’usine, devant « la cathédrale« , s’effectuaient la livraison et le dépotage des matières premières livrées en camions et en bateaux. On y trouvait : du suif de bœuf, des corps gras végétaux comme l’huile de coprah, l’amande du fruit de palme, les huiles d’arachide, l’huile d’olive. Mais également des produits réactifs comme la soude et la potasse. Écoutons les impressions :
«En arrivant le matin au bureau, je me souviens de l’odeur caractéristique qui régnait dans la cour. Il me semblait qu’une petite brume y séjournait toute l’année. Des fûts traînaient un peu partout. Au sol, une épaisse couche de gras qu’il fallait traverser pour monter aux bureaux qui étaient planchéiés».
Il faut savoir que le laboratoire de la savonnerie analysait toutes les marchandises à la livraison, suivait les produits en cours de fabrication et contrôlait systématiquement les produits finis. Des ouvriers qualifiés assuraient eux-mêmes en plus des contrôles du laboratoire, des analyses constantes dans les ateliers afin de garder au savon toutes les qualités recherchées. Et, il y avait le savoir-faire du savonnier, il se souvient :
«On goûtait le savon, si il piquait, trop de soude, trop salé… C’était déjà bien dégrossi avant d’aller au labo».
La fabrication du savon se perfectionne. Les méthodes de blanchiment des corps gras, elles, ne changent pratiquement pas. Par contre, l’installation de saponification continue, remplace l’ancienne méthode de cuite des savons en chaudrons. Après filtration, les différents corps gras sont mélangés et envoyés en continu dans un autoclave, où, en présence de soude, s’effectue la réaction chimique de saponification. Le mélange de corps gras (animaux et végétaux) plus la soude donne du savon et des eaux glycérineuses. Ces dernières sont traitées par acidification, décantation, neutralisation et filtration. Fabrication très complexe pour obtenir la glycérine. Autre changement, le séchage. Avant, le savon chaud et liquide coulait dans des cadres de dimensions variables. Ces cadres serrés par des plaques étaient refroidis par de l’eau. Avec la méthode Mazzoni le savon brut est envoyé dans une unité de lavage puis centrifugé. On obtient une pâte de savon qui est déshydratée. C’est très complexe… mais il sort sous forme de barres continues et de formats variables.
Elles sont coupées automatiquement à la longueur désirée. L’usine emploie 300 personnes, 155 femmes et 145 hommes. A la fabrication on ne trouve que des hommes. Dans l’atelier de conditionnement nous rentrons dans un domaine féminin. La frappe des morceaux de savon leur donne la forme définitive ainsi que la marque. Modernisme, c’est maintenant la machine qui fait ce travail. Mais au temps du savon le chat ambré se sont encore les ouvrières qui le mettent dans son emballage. Et elles se souviennent :
«Du temps de Catox c’était dur, mais nous étions autour d’une table. Avec le tapis roulant, fini la causette, la chaîne n’attend pas, il ne faut pas s’arrêter. Dans le tas, il y avait bien des garces qui voulaient en faire plus, car nous touchions des primes. Mais dans l’ensemble, il ne fallait pas se plaindre. En fin de semaine, la paie était distribuée dans les ateliers. Après c’était relâche, cela donnait l’occasion de souhaiter une fête, un anniversaire avec des gâteaux et un verre à la main. Mais nous savions aussi être toutes solidaires dans la peine d’une copine».
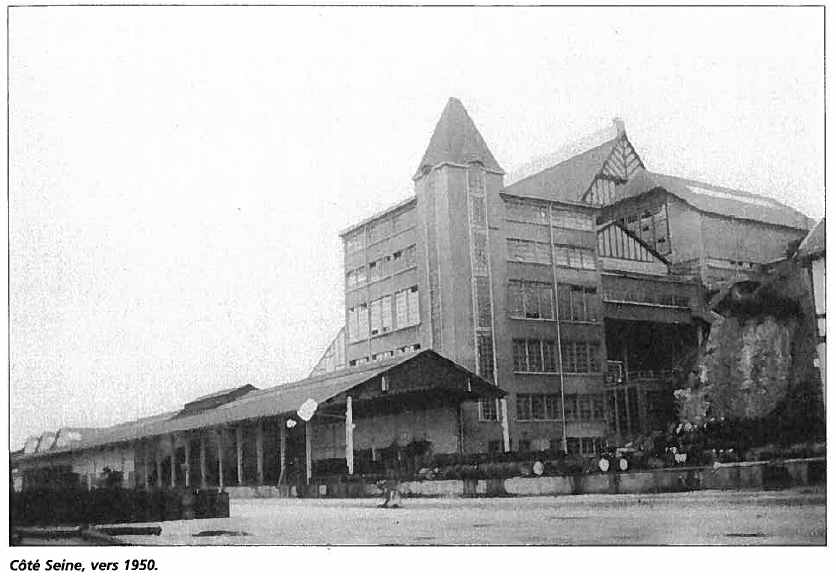
Malgré les soins apportés à la fabrication, les yeux exercés des emballeuses repéraient les défectueux et elles retiraient 5% des savons qui étaient recyclés. Nous sommes au bout de la chaîne, le savon arrive au conditionnement. L’emballage se fait sur plusieurs lignes. L’emballage et la mise en étuis sont automatiques. Les machines enveloppent sous pellicule PVC ou sous étuis. Les expéditions se font principalement par la route, quelquefois par fer. Un stock de 1000 à 1500 tonnes de savon reste en réserve.
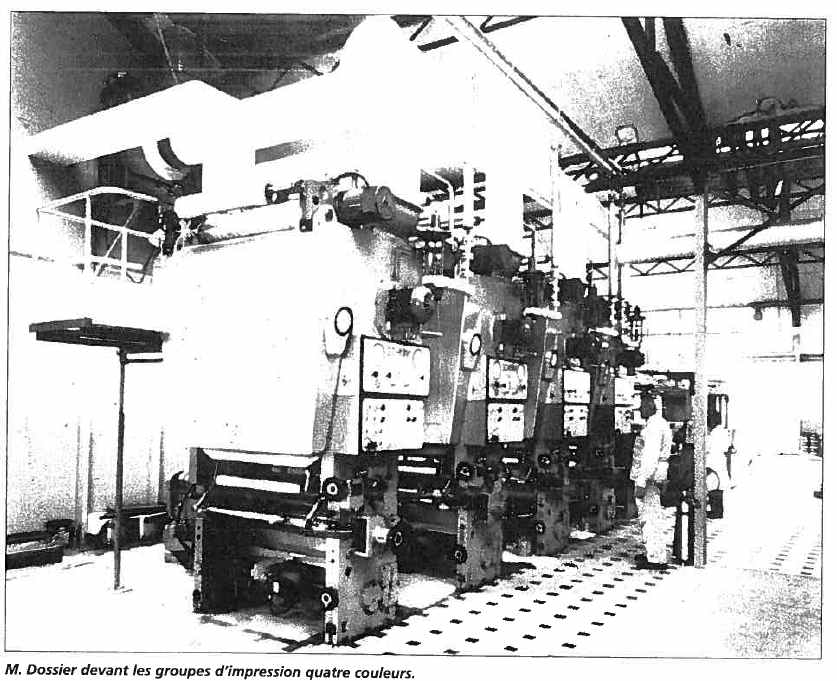
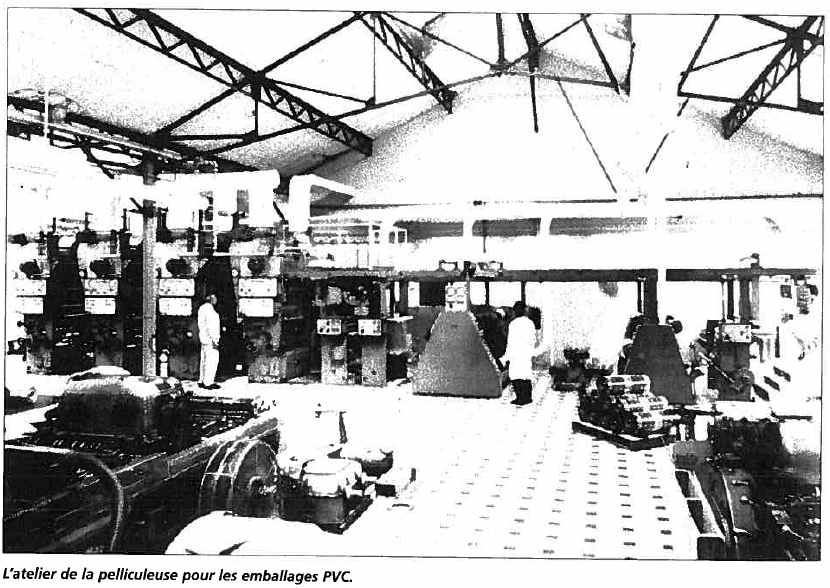
La savonnerie de Yainville imprime les emballages du groupe Unipol. Elle dispose de deux machines Typo-Offset qui peuvent sortir de 300 à 600 emballages imprimés quatre couleurs par heure, et une machine Hélio, très moderne qui permet l’impression en quatre couleurs des pellicules, cartons et papiers. Cet atelier imprime environ 100 tonnes de papier carton par an, et autant de pellicules Cellophane, PVC et polypropylène. De plus un outillage complémentaire permet la découpe des bobines de pellicules et la confection des étuis en carton. Pendant une dizaine d’années quinze personnes travaillent dans cet atelier. Trop performante cette imprimerie… car les choses ne durent pas. Les gros fournisseurs de PVC, vendent à la savonnerie le PVC brut, plus cher que le prix de revient de celui imprimé à Yainville. Donc l’imprimerie n’est plus rentable et il faut acheter leurs produits tout imprimés.
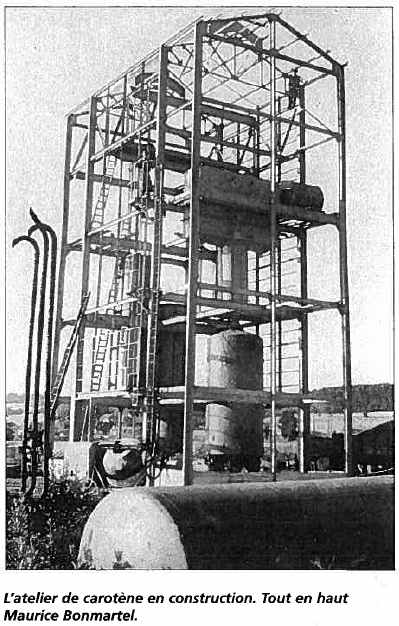
Le même problème s’était posé avec le carotène. Une expérience malheureuse qui débute en 1954, par la construction d’un atelier. On trouve ce produit dans l’huile de palme. La savonnerie en fabrique. L’essai est bon, Yainville en fabrique de ce carotène. Ils ont réussi. On tire 1 litre 500 de ce produit pour 1.000 litres d’huile de palme. Le produit vaut son pesant d’or, il se vend. Puis une société suisse invente le carotène de synthèse. Le savoir-faire de la savonnerie ne sert plus à rien, les prix chutent, on stoppe la production, qui n’aura duré que quelques années.
En 1967, les Nouvelles savonneries françaises, rachètent Gilot et Alésia deux petites sociétés de production de savon de toilette, situées dans la région parisienne. Yainville construit un nouvel atelier de savonnetterie, destiné à fabriquer du savon de toilette sous le nom de Gilésia. Il sera vendu en parfumerie et en pharmacie. La production annuelle augmente rapidement de 150 tonnes par mois, elle arrive à 2.200 en 1987. L’usine fournit plus de 90 clients et vend 1.000 sortes de savonnettes. De la fabrication du savon de Marseille découlent les autres savons. Celui des savonnettes est affiné, parfumé, coloré puis malaxé. De nouveau affiné avant de sortir de la boudineuse. De là elles prennent leur forme définitive. La mise au point de ces produits et la réalisation de modèles nouveaux sont effectuées à Yainville. Le père Pauvy fabriquait des maquettes de savonnettes en bois. Polis, cirés, ces échantillons servaient pour choisir le volume et la forme. Accepté, le modèle était reproduit en bronze. Il y avait des dizaines de prototypes en attente. L’emballage de ces produits de luxe, demandait extrêmement de soin, il s’effectuait à la main.
Une marche continue et régulière d’une telle entreprise demande un service entretien efficace. Des ouvriers qualifiés possèdent un atelier muni de machines-outils capables de palier rapidement à toutes pannes et réparations urgentes.
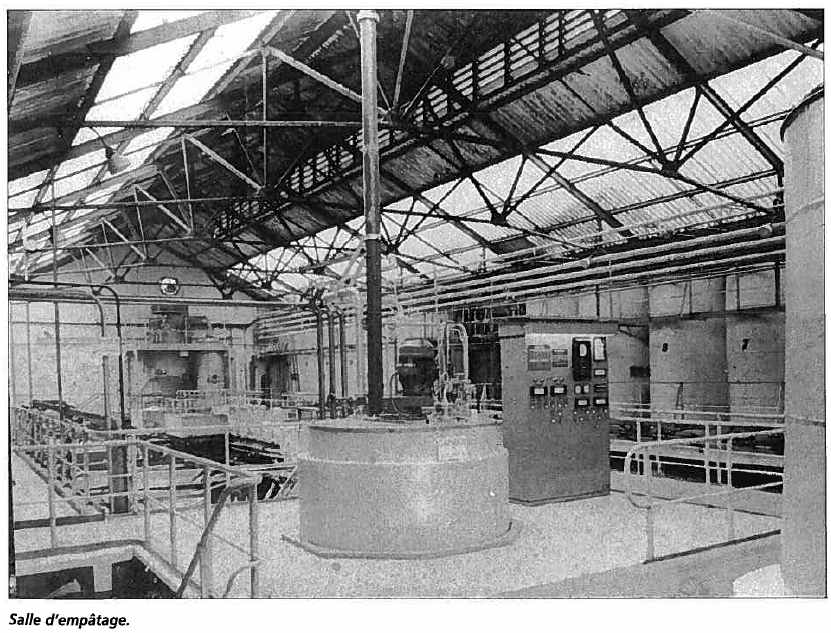
L’effort n’est pas qu‘industriel et commercial et une attention toute particulière est consacrée aux problèmes sociaux. Le Comité d’entreprise organise fêtes de Noël et voyages. Un centre social réunit dans un bâtiment des vestiaires et douches. La cuisine et les réfectoires sont bien agencés. Dans le service médicosocial un médecin consulte. La coopérative, une salle de réunion du C.E., complètent ce bâtiment situé à l’entrée de l’usine.
Depuis les grèves de 1936, la guerre passée, il règne un bon climat social à la savonnerie :
«Il fallait être saoul, et pire encore pour être mis à la porte».
L’usine n’échappe pas aux évènements de mai 1968. Et… écoutons :
«Les gars du Trait sont venus devant l’usine pour nous dire d’arrêter le travail. Nous n’avons pas occupé les lieux, un piquet de grève fut institué. C’était mieux, car les femmes avaient leur mari dans le chantier naval, elles leur portaient à manger. Nous étions en relation avec Marseille, où se situait la maison mère. Mais, comme à l’huilerie, nous nous sommes arrêtés de travailler peu de temps».
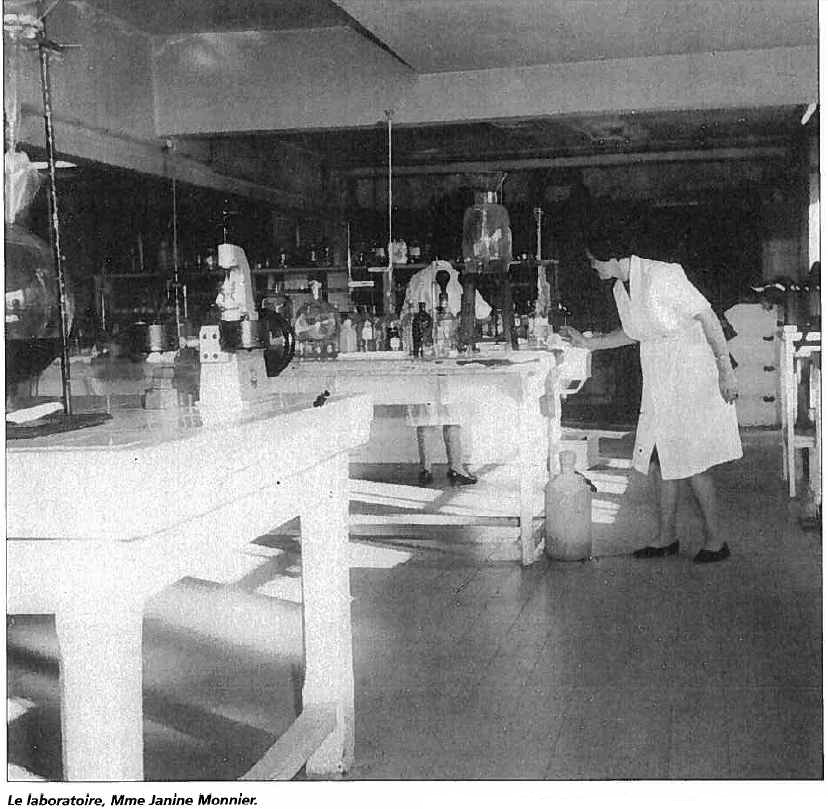
En 1974, une autre concentration industrielle, la NSF (Nouvelles Savonneries Française-Fournier-Ferrier et Gilesta) se regroupe avec la Société Salador, la nouvelle dénomination est : Union Générale des Savonneries. A cette date, l’usine est à son summum. Elle emploie 330 personnes, soit : un directeur, 10 ingénieurs et cadres, 18 agents de maîtrise, 23 employés, 278 ouvriers et ouvrières. Il est bon de citer les chiffres de sa production annuelle qui place Yainville dans les premières savonneries de France : 20.000 tonnes de savon, 5.000 tonnes de glycérine, 7 tonnes de corps gras industriels. Nous sommes dans les décades de la consommation, le temps du plein emploi. On embauche à 18 ans, le recrutement s’effectue dans le cercle de l’usine. On reste en famille, entre gens de connaissance. Les salaires suivent l’inflation. Les primes de vacances, de fin d’année, de rendement sont intéressantes mais aujourd’hui on regrette leur non prise en charge dans le calcul des retraites. Tous continuent d’œuvrer dans le souci de la qualité. Les savons le Chat répondent aux besoins de la clientèle. Les grands parfumeurs confient la fabrication de leurs savons. Les industriels de la chimie apprécient la glycérine. On parle d’écologie, d’environnement et le bon vieux savon de Marseille reste encore la seule façon de laver sans polluer. Pourtant, les Français vont consommer de moins en moins de savon, la progression des poudres à laver y est pour quelque chose. Depuis la guerre, beaucoup de savonneries ont dû fermer. Elles étaient 300 avant 1939, il en reste une bonne dizaine. Certes d’autres activités comme les produits chimiques à partir des corps gras, compensent la baisse de production du savon. Des produits destinés aux industries de la métallurgie, des pneumatiques et du papier. Jusqu’ici la savonnerie a toujours fait l’effort d’investir, de s’adapter, de créer de nouveaux produits :
«Si nous n’étions pas dans les premiers, on se faisait descendre».
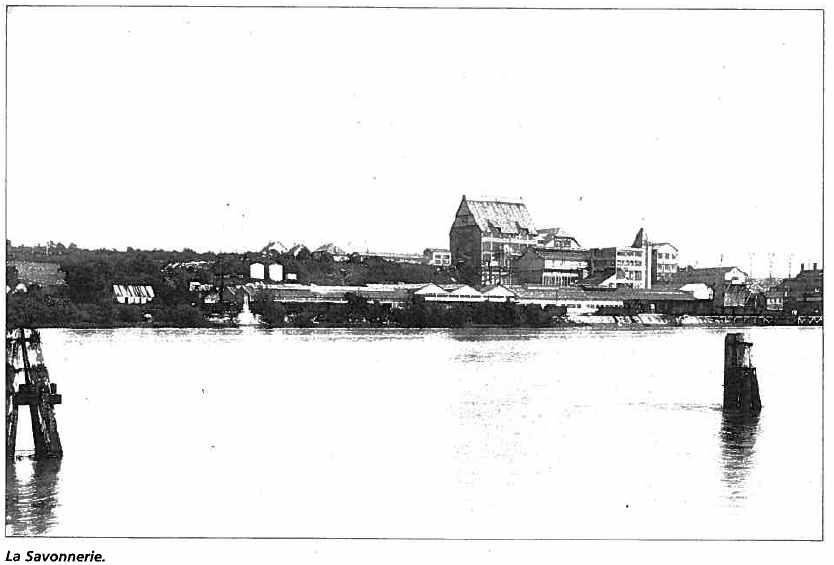
A partir de 1978, les départs en retraite ne sont plus remplacés. Puis on propose des préretraites. Parallèlement le prix des matières premières augmentent. Celui du coprah-palme double. Naturellement les stocks gonflent, car les commandes diminuent. En 1980, on arrête les quarts de nuit…
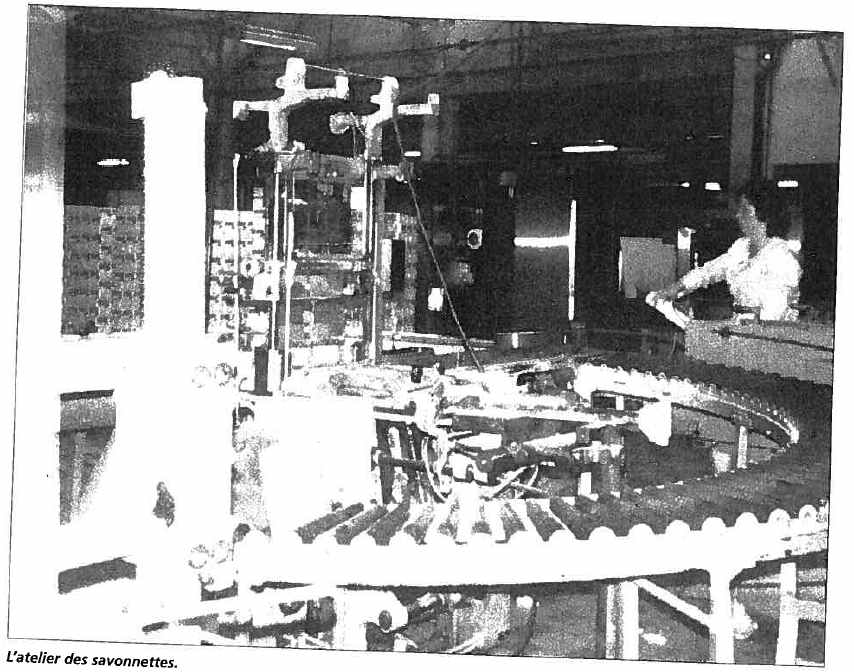
Réservons le mot de la fin à un ancien cadre :
«Mon meilleur souvenir de la savonnerie, celui qui me touche le plus : c’était d’entendre les filles d’un atelier chanter toutes ensembles».
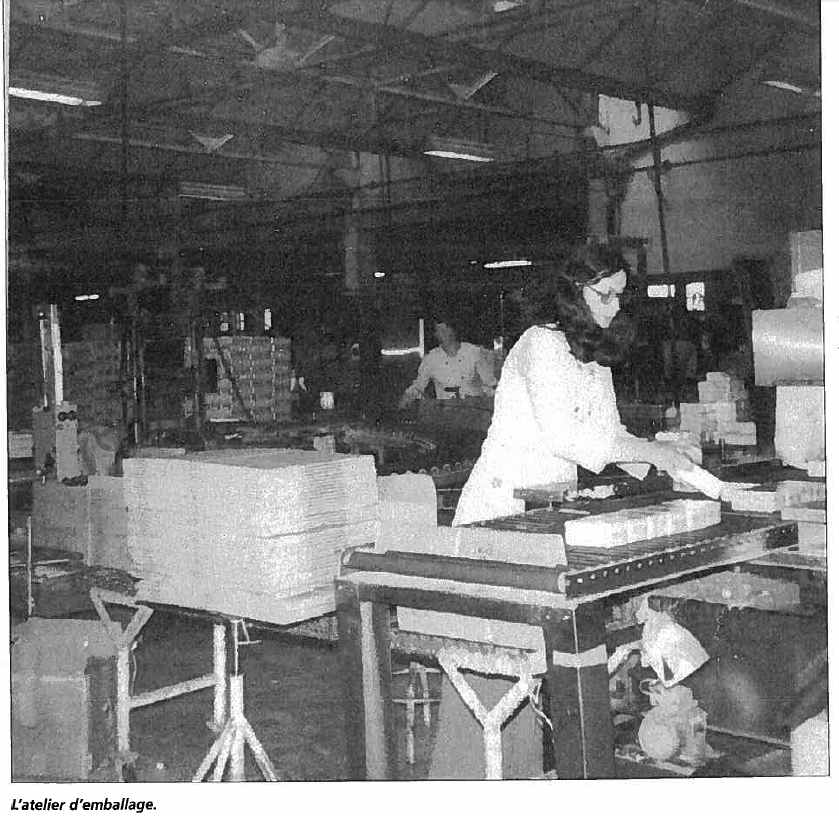
NSF Aujourd’hui :
11/2012 – UrbEx NSF – Part I
12/2012 – UrbEx NSF – Part II
04/2013 – UrbEx NSF – Part III
05/2013 – UrbEx NSF – Part IV
06/2013 – UrbEx NSF – Part V